A New Era Begins: Introducing the Zebra Dry Plate Coating Machine
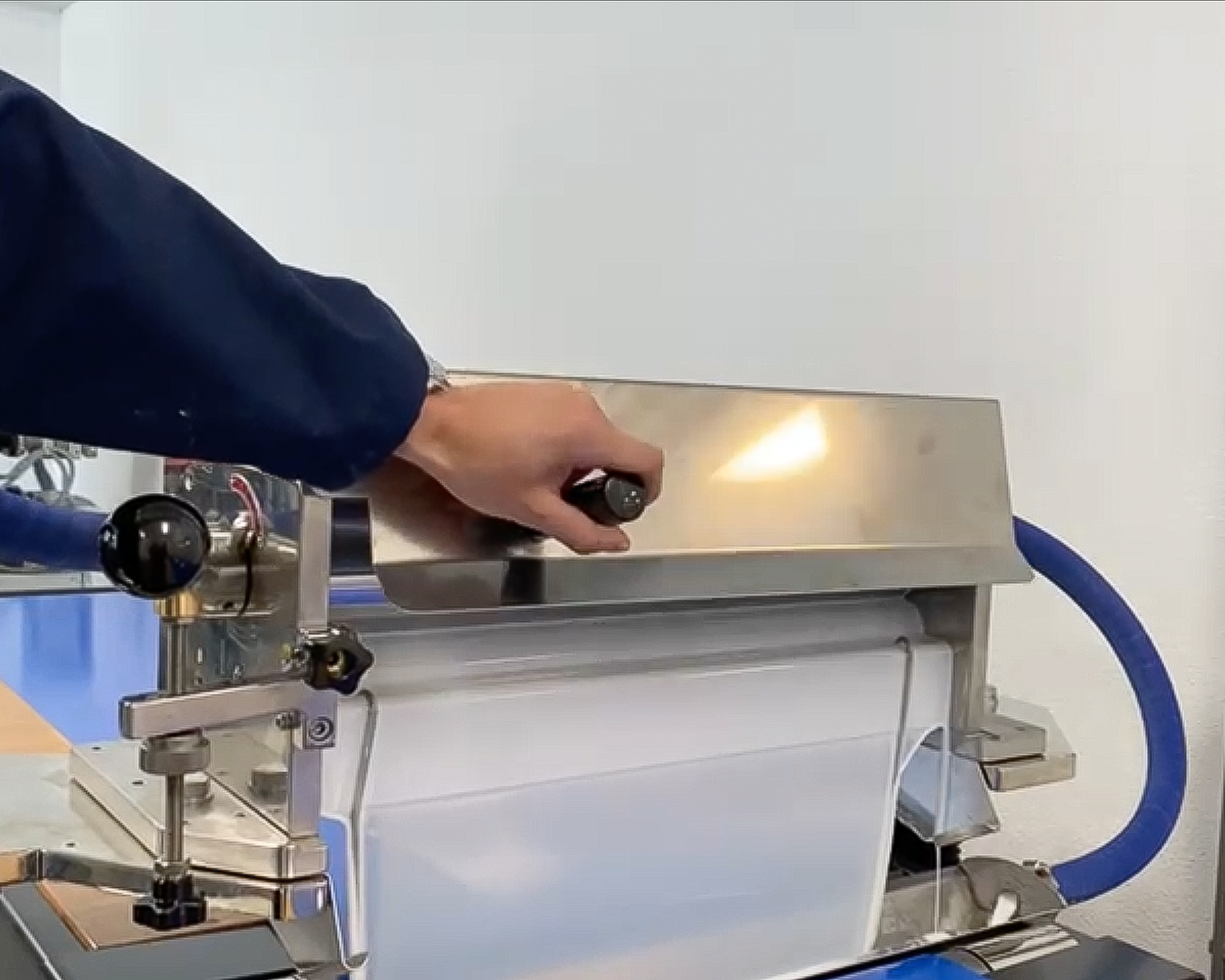
For the past six years, every Zebra Dry Plate you’ve held in your hands has been poured, coated, and crafted by my own two. This was never just about making photographic materials—it was about resurrecting a process. A history. A soul.
I’ve often said that Dry Plate photography is more than technique—it’s a dialogue between light and time, chemistry and craft. And for those six years, I’ve done everything I could to keep that conversation alive by hand-coating thousands upon thousands of plates in our small workshop.
Today, I’m proud—and honestly a little emotional—to announce something that will shape the next chapter of this story:Zebra is getting its first custom-built Dry Plate coating machine.
This is the largest investment in the history of our workshop. A leap of faith, built not on leaving tradition behind, but on giving it space to grow.
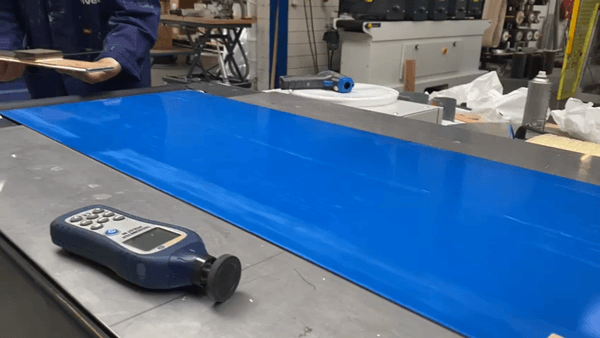
Why We’re Doing This
As some of you already know, keeping up with demand while maintaining quality has become harder and harder. The truth is, I love hand-coating. But over the past year, I’ve reached my physical and creative limits.
I’ve had to turn down requests, delay experiments, and postpone projects simply because I lacked the time. I often found myself dreaming of what could be: plates in new sizes, faster emulsions, direct positives, color tintypes… but dreams need space to breathe. And coating thousands of plates a week by hand doesn’t leave much.
This machine is not a way out. It’s a way forward.
Why Now?
Building a coating machine specifically for silver gelatin emulsion on glass is no small feat. It took us two years of trials, failures, and prototypes to get here.
We tried it all—roller coating, spray heads, spin coaters, slot dye techniques. Some ideas made it to a working prototype, others barely got past the drawing board. One spray coating system even involved magnetic valves and sensors mounted to a homemade conveyor belt. It was beautiful chaos—until we discovered the emulsion would harden mid-air into snowflakes before ever touching the glass 😀
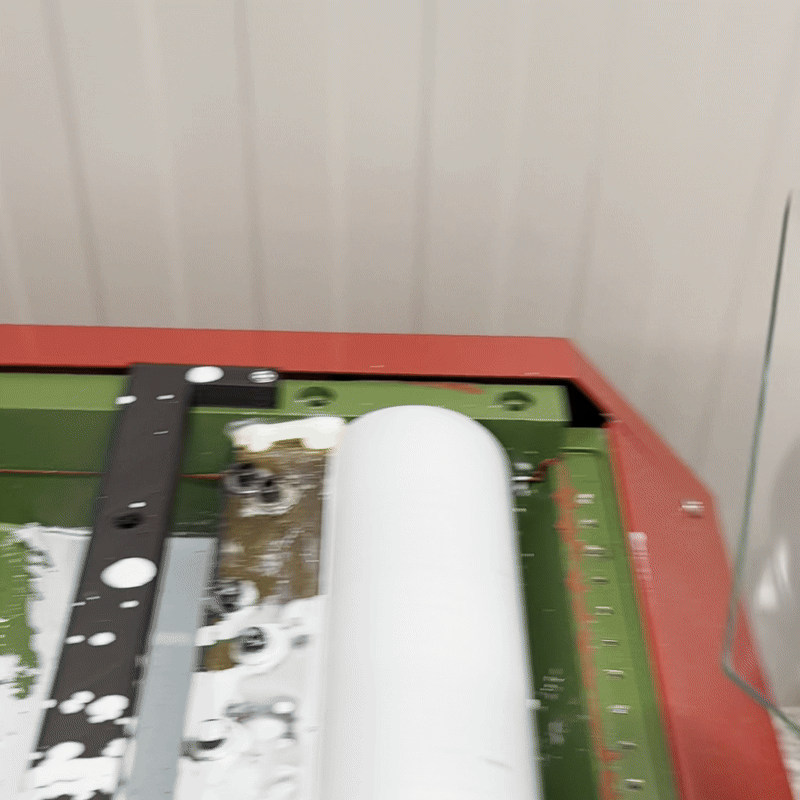
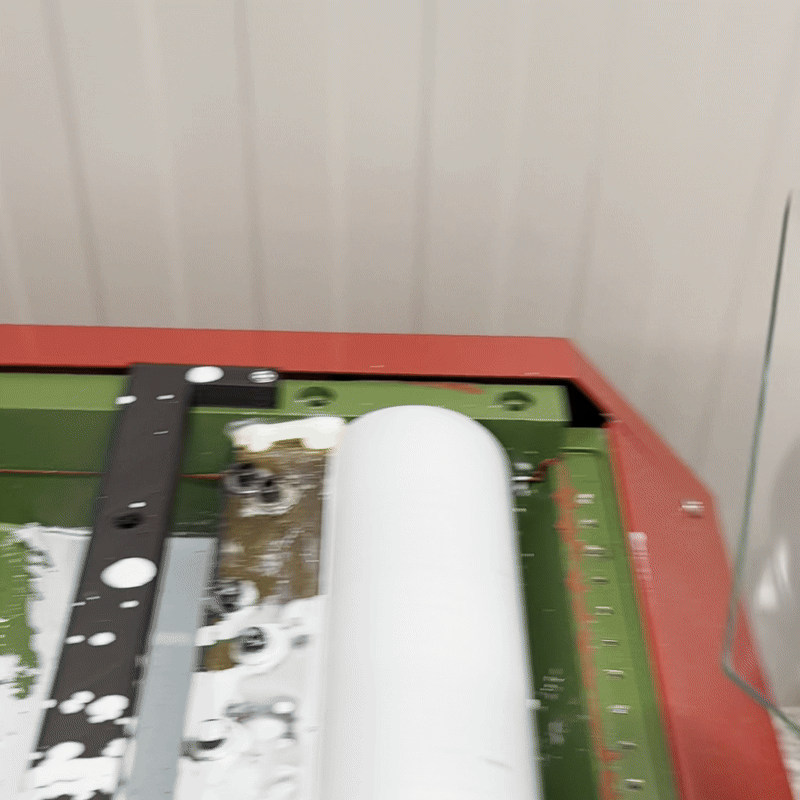
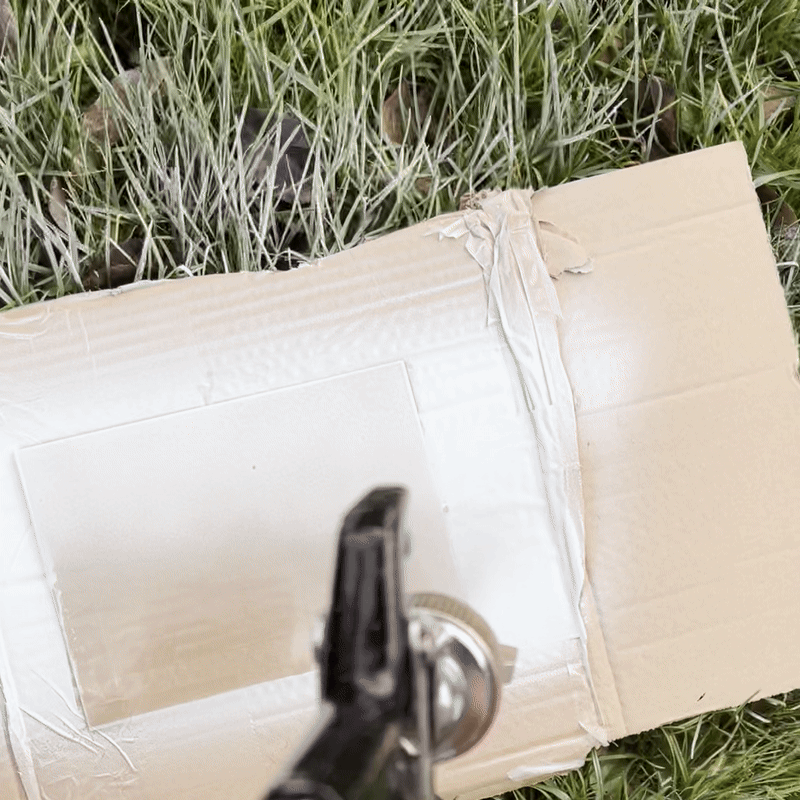
We even looked back into the archives of photographic history, trying to recreate machines used during the golden era of dry plates. But here’s the thing: those historical machines were built for massive industrial-scale production—often operating in full-size factories with large teams and very different infrastructure. Simply copying them wasn’t realistic or cost-effective on our scale. Their complexity, rigidity, and sheer size didn’t align with the adaptable, artisan-driven model we’ve built at Zebra. At this point I would also like to thank Mark Osterman for providing us with his sketches, photos and book references!
Through all this, one truth became clear: there are no shortcuts. High-quality photographic emulsion demands precision, temperature stability, and impeccable cleanliness. It demands a machine that treats this process not as a factory job, but as a craft.
That’s why we partnered with a company to design a custom coating machine tailored to Zebra’s specific needs. Heated reservoirs, chemical-resistant components, precision flow control—it’s all there. And soon, it will find its place in a brand new 40m² darkroom built to house this beast.
What This Means for the Plates
The impact of this machine isn’t just practical—it’s transformative.
- Precision like never before: The machine will lay down ultra-thin, consistent emulsion layers, allowing for better sharpness, smoother tones, and more even development across the plate. Ideal not just for negative making, but also for advanced processes like reverse development into direct positives—a direction we’re actively exploring.
- More formats, more freedom: It’s built to handle plate sizes up to 355mm in width. This opens up possibilities for custom orders, limited runs, and perhaps even experimental substrates like tin or aluminum. (Anything larger than that will still be coated to order by hand!)
- Different types of plates: With the precision and control that machine offers, we’re also preparing to experiment with entirely new types of plates. Imagine cyanotype on glass, holographic plates, and other hybrid or experimental surfaces—crafted with the same attention to detail Zebra has always stood for. This opens doors not just for photographers, but for educators, artists, and researchers as well.
- Scalability with integrity: For the first time, we’ll be able to expand our reach, carefully and respectfully. We’re quietly exploring how Zebra Plates might become available through select analog photography suppliers around the globe—not mass-market, but meaningful partnerships with people who share our values.
If you’re a photography shop or analog gear reseller interested in carrying Zebra Plates, we’d love to hear from you. We’re open to collaborations that help us bring this craft to a wider audience while staying true to our roots.
Reach out at zebradryplates@gmail.com and let’s talk.
Hand-Coated Plates Aren’t Going Anywhere
Let’s be clear: this machine does not mean the end of handmade Zebra plates.
I will continue coating plates by hand—both for myself and for those who value the labour and mastery that goes into them. There’s something magical about a hand-poured plate. Something soulful.
If you’ve ever wanted to experience one for yourself—or simply support our work during this big transition—now’s a great time to place an order, as hand-coated Zebra plates won’t be around forever. Every plate ordered directly from us helps keep this dream alive and self-sustained.
Your support means everything.
-
Zebra 4×5 Wet Plate Holder V294,84 € inc. U.S. import fees
-
Zebra Standard 4×5 Dry Plates41,56 € inc. U.S. import fees
-
Zebra All-In-One Pocket Safelight25,47 € inc. U.S. import fees
What We Learned Along the Way (And Why It Matters)
This journey taught us more than how to build a machine. It reminded us that innovation and tradition aren’t enemies. They’re partners.
Each failed prototype, each bubble in a test coating, each night spent troubleshooting heating systems or pump materials—it all reaffirmed something fundamental:
Analog photography isn’t stuck in the past. It’s built on it.
We don’t need to recreate the factory systems of the early 20th century. We need to reimagine them with care, with craftsmanship, and with respect for the materials we use and the people we serve. That’s what this machine is about.
Looking Forward: One Step at a Time
There’s still work to do. The new darkroom is under construction. The machine is in the final build phase expected to arrive in early May. Once installed, we’ll spend time calibrating it, running tests, and dialing in the magic before any machine-coated plates leave our doors.
To everyone who has supported Zebra—from the first test batch to the latest Kickstarter: thank you. This moment belongs to all of us who believe in the value of doing things the right way, even when it’s the hard way.
Here’s to tradition. Here’s to innovation. And here’s to a plate that captures more than just an image—it captures a way of seeing the world.🖤
Nejc & the Zebra Team
Loving the innovation and quest for a better product without destroying the history of the craft. Wishing you the best, Tom
Congratulations on your quest for excellence in everything you do. I have no doubt this new coating machine will be a game changer for Zebra and for us, the users. Looking forward to at least a full Ortho or even better, a panchromatic plate. Best of luck.