Welcome to the New Dry Plate Era!
Just like for Standard Zebra Dry Plates I put together in detail the user manual for the newly released Zebra Dry Plate Tintypes as well. Since Tintype Dry Plates have been brought back to light pretty recently there is for sure much more to rediscover and explore! Soon many of you will get your own box of plates to enjoy and experiment with so I encourage you to report back your findings, ask questions and share your thoughts as only this way we can gradually expand this manual from which the whole Dry Plate community can benefit from. Thanks!
HOW DRY PLATES CAME TO BE?
First mentioning of Ferrotypes more commonly known as Tintypes goes back into the 1860s when French photographer, Adolphe-Alexandre Martin in the hopes of simplifying the work of engravers discovered Tintypes. His main goal of improving Ambrotypes did not go according to plan so what he did was he replaced glass with a tin plate and came to a remarkable discovery but since this what not what he aimed for he never realized the commercial potential of this technique. It was in the following years with the work of Hamilton Smith and others when Tintypes really started to take off. The process was faster and more accessible to amateur photographers of the era, so its popularity exploded from the mid to late 18th century. Its main feature was a direct positive image so we could even say Tintypes were the polaroids of the era. Even after new more refined processes came to replace the old ones Tintypes remained the staples of photo fairs to this day.
ZEBRA DRY PLATE TINTYPES
Zebra Dry Plate Tintypes deliver an impressive positive image on black surface with the finest grain quality. Overall they are very similar to a more well known Wet Plate version with a few advantages. Because they are coated with Silver Gelatine emulsion which is then dried, plates can be used for months and developed whenever you desire just like with Standard Dry Plates. No rushing and portable darkrooms, all you need is a special developer mixture to achieve a whitish negative. Just like Standard Zebra Dry Plates also these are hand coated (poured) with ultra fine grain silver gelatine emulsion that is sensitive only to UV and blue light. Contrast of the plates is moderate to high. Plates are rated at ASA 2 under winter lighting at middle latitudes, but as with other primitive processes, the effective speed of the plate will vary for a few stops depending on actual UV levels. Zebra Dry Plates are completely hand made and therefore kept to the highest standard of excellence and embody all the latest improvements.
STORAGE & SHELF LIFE
I advise you to store the plates the same way as it’s recommended with the film. Meaning you should keep them in a dry and cool place with temperatures at around 13°C or lover and humidity below 60%. To put it simply, storage in the fridge is perfect. I would not recommend you to store them in the freezer though as when you take them out the condensation from the temperature may cause the emulsion to swell and bond to wrapping paper!
How long do they last for?
It’s like with film the fresher the better but with my experience if stored properly they will last for at least 2 years without any fogging or speed loss!
HANDLING & LOADING DRY PLATE TINTYPES IN THE THE PLATE HOLDER
Start by opening the box of Zebra Dry Plate Tintype Plates under Red Safelights. Inside of the box plates are protected from the light with a sealed black dark bag. Remove the seal and open the bag. Inside you will find plates individually wrapped into acid free archival paper. Gently pull the individual plate out of the stack and start unwrapping it. Just like with any other photographic material you should not touch the emulsion side! You should handle the plate by the edges
Which is the emulsion side?
Plates are wrapped in the protective paper emulsion side down. So when you unwrap and flip the plate around this is the emulsion side. Otherwise upon carefully examining them you will notice that one side has a metallic shine to it and the other is coated with a thin white film.
How to load the holder?
Zebra Dual Glass Dry Plate Holder (or any other dry plate holder)
Before turning off the lights and loading the plates in you should keep in mind that these tin plates are much thinner(0,6mm) than Standar Zebra Dry Plates (2mm) so in order to secure the image in place and get it sharp you need to insert an adapter. What the adapter will do is lift up the plate back into the correct focus plane. You can get yours in the Zebra Store.
Once you have the adapters in turn off the lights pull out the double dark slide from the holder and slide or place the plate inside. If you are using Zebra Dual Plate Holder slide the plate into the slots emulsion side facing up. After you have the plates in slides must be carefully shut closed.
Zebra Wet Plate Holder (or any other wet plate holder)
Wet plate holders are pretty straightforward to use with these as no adapters are needed, only a big enough spring on the back of the holder to keep the plate pressed to the focal plane. If using Zebra Wet Plate Holder simply open the magnetic lid, unwrap the Tintype plate, insert it in the carrier and pop the magnetic lid back into its place. Just make sure that you place the plate into the holder emulsion side facing down or you will end up with no image.
Once your plates are loaded a very great care must be taken that you fold the black bag with remaining plates in the starting position, reinstall the seal and place the wrapped plates back into the box as the sudden opening of the dark room door, or the slightest admission of daylight, would effectively spoil the whole box of plates, making them fogged and therefore useless.
EXPOSURE OF THE PLATE
EXPOSURE OF THE PLATE
The correct exposure of Zebra Dry Plate Tintype to light in the camera along with development is of the greatest importance since most of the failures in positive making are due to incorrect exposure. Exposure depends upon many conditions such as: The speed (ISO) rating of the plate, amount of UV light present in the scene that depends on the following parameters: time of the day, the season, latitude and altitude Quality and strength of the light Kind of lens and aperture Extension of the bellows Nature of object to be photographed
Selecting the Subject:
The first matter of importance is to select the subject to be photographed as for instance, Study of Sky or Clouds, Snow or Open Sea scenes or far distant landscapes require the shortest exposures, while landscapes with heavy foreground, Badly-lighted river-banks and dark objects must be exposed longer, and interior portraits, building interiors, etc… usually need even longer exposure. When selecting the correct exposure a great deal depends on photographers judgment and experience, which can only be acquired by continued practice. In exposing a plate, probably the best guide is your own eye but for those starting out there have been multiple ingenious exposure tables obtained by different parties throughout history to help selecting correct exposure. For those of you who already have experience with Dry Plates this will be fairly easy. But for those who will be using Zebra Dry Plate Tintypes for the first time I came together with a Zebra Exposure Guide based on exposure guides compiled by Malcolm Dean Miller. These Exposure Guides will help you select the right exposure during different months of the year, times of the day and subject being photographed in order to nail your Tintypes everytime.
MONTHLY EXPOSURE GUIDES:
Monthly Exposure Guides where adjusted according to the Slovenian monthly UV Index levels listed in the chart bellow. Depending where you live monthly UV levels can be completely different to ours so adjust exposure guides accordingly.
Once you gain confidence and understanding of how the emulsion “sees” under different circumstances you can go ahead and start using a light meter with simply adjusting the speed. You can also use Light Metering Apps and the one I recommend and use on a daily basis is Light Meter Free that allows custom ISO inputs starting with 1 and up.
TEST EXPOSURES
To test the correct speed of the plate and ascertain correct exposure it’s advisable to make a test by making a step wedge or exposing three plates, one rather short, the second twice and the third three times as much time, and compare the manner in which the image appears during development. In an underexposed plate it will take longer for the image to appear and there will be a lack of detail in the shadows. Overexposed plates show full detail but lack contrast; prolonged development will increase the contrast as well as the density.
KEEPING A RECORD
When you are starting out it’s advisable to keep notes with a record of all exposures and memoranda made of conditions of light, time of the day, etc. This is highly necessary especially if you have shot more than a few plates as you can with your first developed plate determine whether or not you have over or under exposed and adjust the development of remaining plates accordingly. Whenever you are trying something new the temptation to just go out and photograph whatever interesting comes along is very high. But remember you don’t have an endless amount of exposures left so calm down and take your time to run some exposure & development tests that will help you with following exposures. When making exposures keep in mind that blue sensitive emulsions “see” much differently than we do and that requires a bit different approach than you are used to with modern film. There are a few things you need to take into consideration like the amount of UV light present in the scene, color of the subject, color of light…
ADDITIONAL EXPOSURE COMPENSATIONS
TIPS FOR SHOOTING INDOORS
When making exposure indoors under artificial lights (Tungsten, Fluorescent, LED) where there is very little to none UV light I recommend you to use a light meter, meter at box speed (ISO 2) and add 3 stops of exposure. Unless you are working under very strong lights there is a very high chance for your exposures to quickly be several minutes long and reciprocity failure will have to be taken into account as well.
RECIPROCITY FAILURE
Since Zebra Dry Plate Tintypes are coated with ultra fine grain emulsion reciprocity will have no visible effect up to 1min of exposure. After 1min I recommend extending your exposure time for 50% or to double your exposure time with exposures over 2min.
BELLOW EXTENSION FACTOR
Whenever you want to focus on something close to the camera your bellows will extend wide. Because of the long distance between the lens and film plane some light will get lost and you will have to account for the so-called bellows extension factor that gets added to the exposure. This is where you have to pull out a ruler from your camera bag and start measuring.
The equation is very simple and it goes like this:
Bellow extension squared divided by the lens focal length squared. Measure your bellow extension from the lens board to the focal plane. For instance if your bellow extension is 260mm or 67.600mm squared divided by the focal length which is 235mm or 55.225mm squared you get a factor of 1,224 which you can round to 1,2 and this is your bellow extension factor. You need to multiply your exposure with the factor of 1,2.
EFFECT OF ALTITUDE ON THE SPEED
If you plan to carry those heavy glass plates higher up in the mountains you have my admiration but note that with higher altitude also UV levels increase. It depends where in the world you are but the rule of thumb is that with every 1000m of altitude UV levels increase by 10%. If you are shooting in the mountains or at higher altitudes the exposure of Zebra Dry Plates that are mostly sensitive to blue and UV light should be adjusted accordingly. You should reduce your exposure time by 10% with each 1000m above 500m of elevation.
In Alps where UV levels are even higher you can reduce your exposure by 15% with every 1000m above 500m of elevation.
DEVELOPMENT OF THE POSITIVE
The beauty of Dry Plate Tintypes is that you don’t need to develop them immediately after the exposure like with wet plates. Instead you can take your exposures and return from your trip or studio and develop the plates without rushing the next minute or in a month.
When releasing the Zebra Dry Plate Tintype plates my main goal was to make this beautiful technique available for others to enjoy and experiment with. It took quite a while to figure out how to prepare and pour the tin plates but to be honest this was the easiest part of commercialisation. Much harder part was to figure out the simplest possible processing procedure both when it comes to chemicals and usability. On the molecular level it’s still pretty complex so if you would like to understand what is going on and how black negative turns white read carefully 🙂
Development of a direct positive on black tin plate is a classical Develop, Wash, Fix, Wash by inspection process but it requires some consistency and patience. But don’t let this scare you, after all it’s still all chemistry that is under your control so by carefully following the rules enumerated below your success is certain. Like I mentioned in the beginning Dry Plate Tintypes are a fairly “new” invention so also the use of developers is limited. I am sure with time when more and more of you start to use these plates you will come up with your own developer formulas so please report back on your findings so I can include them in this user manual for all of us to learn. Despite this being a fairly recent invention there are actually a few developer formulas that one can try. Most of them were formulated by Lee Lira and others in our FB group. Some developers are fairly simple to mix and use and the others are much more complex. The one I am about to dissect is by far the most simple to mix, use and the least hazardous for your health and environment.
This developer procedure is proven to work well with Zebra Dry Plate Tintypes so it is not a guarantee it will work for your plates and emulsions. However I will explain things in great detail to share my knowledge and hopefully encourage you to experiment on your own, to play with the quantities, developing time, exposures etc. This is a fairly new process with much more potential that is yet to be discovered and I hope premade Zebra Dry Plate Tintypes will help with that.
How the White Negative(positive) is achieved?
To answer this question we have to look super close to see the dance of molecules.
When you hear the word positive in the analog circles you probably first think of the time consuming and tedious reverse development procedure. But good news this has nothing to do with Dry Plate Tintypes they are much easier to process than that!
Our main goal when it comes to Tintype positive is to develop it in such a way and with such chemicals that would turn what is normally a black negative into a white negative which on black surface reads as a positive. In order to understand that we first have to look at what goes into the developer itself. Before I start I would like to point out that this developer formula was first introduced to us by Lee Lira but was later tweaked and tuned to suit my emulsions needs.
Water
If I say no water no developer I think I said it all 🙂
Joke aside, water is necessary to mix and dilute the chemicals in. If you are convinced that tap water you have is okay to use, go ahead if not I recommend you to use distilled water as you really do not want to add another variable to this complex developer we are about to mix. Temperature of the water or whats soon to become developer is of great importance as well. The warmer the water the faster the reaction. I prefer using 20C for all of my plates.
Developer
Developing agent is what makes the reaction start. Adding more means your image will develop faster and your developing times will be shorter and vice versa. I am telling you this because the amount of Developer added plays a crucial role with the uniformity of a positive tintype image as I will explain later on.
*Recently I have heard that the Kodak version is pretty hard to get in some countries but you can always use alternatives listed in our Developing Chart.
Ammonium Thiocyanate
Ammonium Thiocyanate serves as a complexing agent that during development extracts the silver and deposits it on the surface of the plate which at the end appears like a white positive on a black background. The amount of ammonium thiocyanate has to be finely tuned to the specific emulsion you are using. For Zebra Dry Plate Tintypes only 3g per 300ml is needed and you can purchase it directly in our store right HERE.
Ammonium Thiocyanate is not the nicest chemical out there so it has to be handled with care in a good ventilated room, with some gloves on!
Okay guys now that we know what ingredients go in the developer and what is their purpose lets go thru the complete developing procedure and formulas for getting that perfect Zebra Dry Plate Tintype Positive
ZEBRA DRY PLATE TINTYPE DEVELOPER FORMULA (updated on 18.10-2023)
In hopes of making these plates commercially available my main goal was to find a developer formula that is easy to prepare and easy to use so anyone can find the chemicals they need to mix them together and enjoy this magical process. As you can see we made it as there are only three ingredients that have to be mixed together in order to get a Tintype Developer. I say this because the idea for this HC-110 developer mixture was first brought to light by Lee Lira and then fine-tuned by me for my specific emulsion.
As many of you know, we’ve long recommended HC-110 as our primary developer. However, as of late, it’s become increasingly difficult to find. But don’t worry because we’ve been hard at work to find excellent alternatives for you, and you can now get them directly from the Zebra Store!
In our pursuit of the perfect developer options for both Standard Plates and Tintypes, we’ve rigorously tested various alternatives. We are excited to introduce some of our top picks: 510 Pyro, D76/ID-11, Moersch ECO, Bellini Euro HC, Fomatol LQN, Ilfotec HC, and more! Surprisingly, Fomatol LQN, the most budget-friendly option among them, has emerged as the top choice for both negative and positive development!
FORMULA:
300ml of water at 20C
5ml of Fomatol LQN Developer
3g of Ammonium Thiocyanate
*for 8×10 plates or bigger use twice the amount of developer*
TIME OF DEVELOPMENT
TIME OF DEVELOPMENT
Developing time for correctly exposed Zebra Dry Plate Tintypes with the developer formula I mentioned above is 3min. Once you take the plate out of the holder, submerge it fully into the developer and agitate gently for the first 30s.
*don’t be surprised when you see the negative appearing you are on the right track! Silver deposited on the surface will become visible as a positive only after you finish the fixing process when all of the unexposed silver halides are removed.
If properly exposed, the negative should start appearing in about 40-50 seconds, but the development should be continued until you reach the 3min mark. To prevent unequal action and any decomposed particles from settling on the plate and causing spots I recommend you to agitate for a few seconds every half a minute. The plate is properly and sufficiently developed when those parts of the picture which were white in the original are almost perfectly opaque in the negative,—the darkest shadows remaining whitish and unaltered under the influence of the developing solution, and the gradations of tone fully preserved. One tip: plate should be pulled out of the developer right before your last bit of shadows start to come as they are already there but it’s hard to see under faint illumination of the safelights.
The development of a plate which has been properly exposed is a much more simple matter than would appear by the description, indeed, it is almost difficult to spoil a picture which has been nicely timed ; on the other hand, as a beginner you will definitely have to face under or over-exposed positives at some point. In order to still save those positives during development I am sharing these two facts:
There is still hope for the underexposed positives Take a look at this example below which was pretty significantly underexposed due to a metering mistake. I extended the dev. time to 5min30s and was pleasantly surprised how much of the shadows the developer was able to pull out. Informations are there just to give the developer time to find them 🙂
Image which has been greatly over-exposed bursts into sight at once as soon as it gets in contact with the developing solution, and the image gets fogged all over immediately with very little contrast. But do not give the plate time to go so far as this! As soon as you see that the image is appearing way too quickly (for example 10s into development) be ready to pull it out sooner and stop development without delay by rinsing it with clean water.
So whenever you are out in the field deciding what exposure to go for, remember that it’s always better to slightly overexpose and underdeveloped than to underexpose.
Other Tintype/Ambrotype developers that are worth trying out:
Developing Charts for Zebra Dry Plates
Other alternatives:
Rockland Colloid style developer (formula below can be scaled back to make 1l).
For Zebra Plates dilute the developer 1:1 with water and develop for 1 minute and 30 seconds at 20C
*Thank you David Erickson for sharing this!
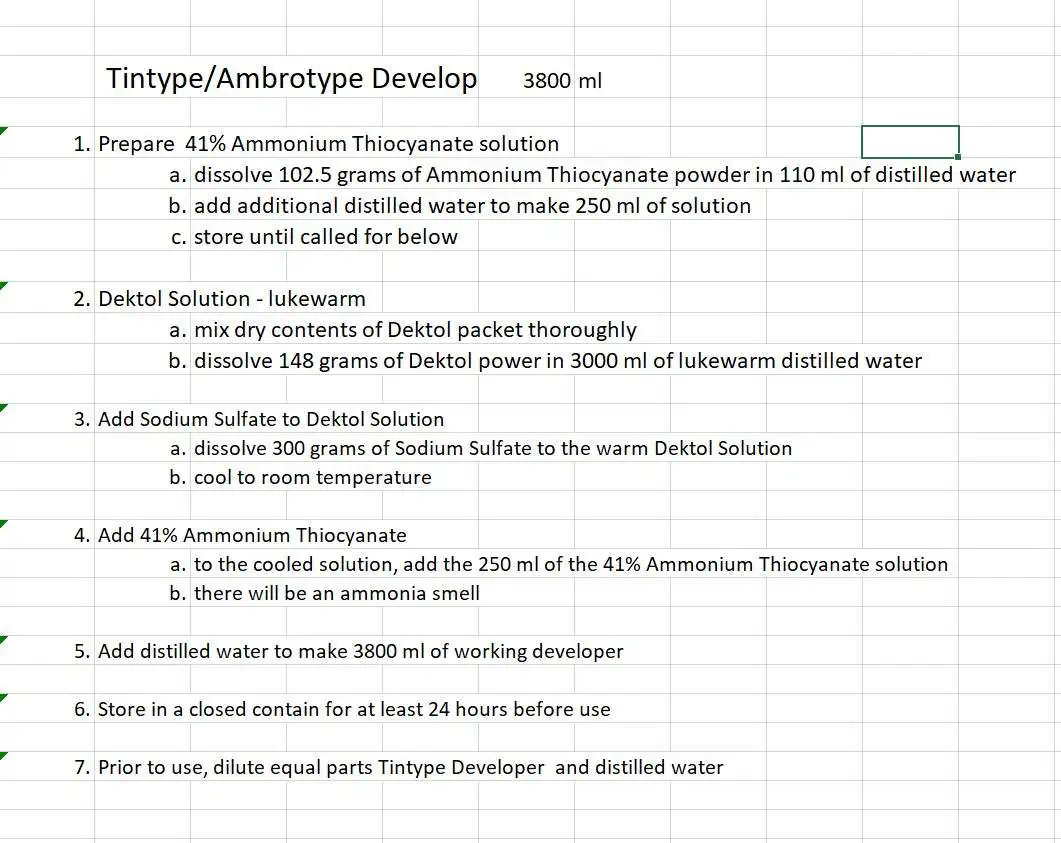
Liranal 6 developer (recipe by Lee Lira)
Mix at 50°C in order listed, make sure each chemical is fully dissolved before adding the next.
Water 375ml
Metol 1g
Sodium sulphite 35g
Hydroquinone 3g
Sodium carbonate 22g (anhydrous)*
Potassium bromide 2g
Ammonium thiocyanate 22-24g*
Water to make 500ml.
For Zebra Plates dilute the developer above 1:1 with water and develop for 1min30s at 20C
If you are successfully using any other developer or dilution please let me know so I can add it to the list. Thank you 🙂
RINSE BATH
After development, move the plate to a water rinse bath for a minute to stop the developers action. You can use the same rinse bath as you do for the film which is in my case water.
FIXING
Before you start fixing the plate you will have a negative on a tin plate but soon it will turn into a beautiful positive. The goal of fixing is to clear away all the whiteness (unexposed silver bromide) from the emulsion so that only the positive remains, sharp, clear, and distinct. There are many fixers out there you can use from simple HYPO to more advanced Rapid Fixers whis is what I recommend and work with. I always fix for at least 5min agitating gently and if using Rapid Fix plate should be cleared by then. You can also fix by inspection and observe when all the white areas are gone, and positive is clearly visible you should continue fixing for another 2min or so. Fixed plate is no longer sensitive to light so you can turn on the lights and proceed to final wash.
FINAL WASH
To insure long life of your image it’s important that you thoroughly wash out all the fixer. I recommend at least 10-15min of washing in running water below 20C. If you are using trays just change the water a couple of times. Insufficiently washed plates can form brown stains and degrade much faster. Addition of PhotoFlo to decrease water surface tension and minimize water marks and drying streaks on positive is recommended but not mandatory!
DRYING
After final wash the emulsion will still be swollen and therefore very delicate so in order to make it bulletproof you have to dry it out again. Zebra Drying rack was made just for this purpose since the plate will be tilted ensuring optimal water drainage and fast drying time without watermarks. Dry the plate in a well ventilated room will take between 4-12h depending on the temperature and humidity level. I do not recommend the use of a hair dryer which can indeed speed things up but remember the emulsion is still swollen and will catch all of the dust and dirt you will introduce when blowing. That dust and dirt will then dry in the emulsion and you will never be able to take it out again only with photoshop.
*While the plate is drying expect some color change as well because the light will reflect differently from a dried emulsion.
SAMPLE OF CORRECTLY EXPOSED ZEBRA DRY PLATE TINTYPE
What does the correctly exposed and developed Zebra Dry Plate Tintype look like?
Below is an example of such a Dry Plate Tintype exposed by myself using an Intrepid 4×5 Camera together with Schneider -Kreuznach 135mm convertible lens. Exposure time was 1/8s at f8 and the plate was developed with the recommended formula for 3min at 20C.
On the left there is a well exposed and developer Zebra Dry Plate Tintype and on the left is a Standard Zebra Dry Plate Negative digitaly inverted for comparison.
A well exposed and developed Zebra Dry Plate Tintype should render a bright positive image with a slightly warm milky white hue. And the amount of details these plates can capture is simply unbelievable as you can see below (sorry for the dust).
SOME BONUS TIPS FOR THOSE WHO WOULD LIKE TO EXPERIMENT
Uniformity of the positive
When it comes to uniformity there are three factors to consider that are in strong correlation with each other. I would like to point out that quantities and dilutions are highly dependent on the type of emulsion you are using so these parameters should be finely tuned in order to get the results you like.
Time
The shorter the development the less time the developer has for penetrating the emulsion and developing all the way through. When you start developing it takes a while before you start to see the reaction. Why? Because the gelatine needs some time to swell and open up to the developer. Parts of the plate that are thicker take longer to swell. This is why I have decided to dilute the Foma LQN 1:59 with water to give the emulsion more time to open up and for the developer to react more evenly.
Developer
Adding too little and your plate will not be evenly developed as the emulsion is usually thinner along the corners of the plate and thicker at the middle. Developer penetrates the thin parts of the emulsion much faster and therefore develops it more. Adding too much and the reaction will be too fast for the Ammonium Thiocyanate to properly do its job.
Ammonium Thiocyanate
Remember ammonium thiocyanate also acts as a silver solvent. It basically slowly eats away silver halides from the image so if too much of Ammonium Thiocyanate is added your thinnest parts of the plate (edges) might be gone forever as it will simply melt it away during processing. Here is an example:
What determines the hue?
Hue is actually determined by the size of the silver particles being deposited on the surface by Ammonium Thiocyanate. Their size determines what kind of hue they will reflect.
Hue is strongly based on the temperature of light that is being shone on to the plate and reflected back into our eyes. Nevertheless tintype positive acts like a silver mirror so if your plate looks incredibly warm like under room lights step outside in the shade and it’s gonna be perfectly white.
Time & temperature
Hue can be determined by the developing time. If ideal, your positives should have a warm milky white hue to them. The longer you develop the warmer the whites. You can control your developing time with temperature but be aware that you need to give the Ammonium Thiocyanate enough time to do its job and form a silver positive. Here is an example of correctly exposed but overdeveloped plate where you can see the emphasized warm hue. Developing time was 4min with the recommended formula.
Amount of Ammonium Thiocyanate
Another very important factor that can greatly affect the hue is the quantity of AT being used. The more Ammonium Thiocyanate you add to the developer the smaller the silver particles will become and the being reflected off them will be cooler. Vice versa the less AT you use the bigger the particles and the warmer the reflected light. Here is an example of a plate that was developed in the recommended formula but instead of 3g of Ammonium Thiocyanate 7g where used. It gave to positive prussian blue hue.
POTENTIAL PROBLEMS AND THEIR SOLUTIONS
Lack of contrast and very dense positive
Lack of contrast is often the consequence of over exposure or overdevelopment.
SOLUTION: it’s obviously shorter exposure but if you are already developing the negative and the whole picture flashes up at once, cut development accordingly.
Thin positive
Thin positive is mostly a consequence of two causes:
-Insufficient development (to short)
-Underexposure
SOLUTION: Develop or expose longer
Emulsion lifts/detaches of the plate
Technically we would call that “ Frilling,” and it’s generally the cause of three things:
– Plate being too warm once it gets into developer
-Your developer is to warm or the temperatures are not the same throughout processing solutions
-You are agitating to aggressively
SOLUTION: Keep all of the processing solutions at the same temperature 20C or lower, agitate gently and work with the recommended developer listed above.
Yellow/foggy spots on the positive
Yellow spots on the dried positive are often caused by left behind fixer deposits after inadequate final wash.
SOLUTION: Make sure to properly wash the plate after fixing it in fresh water for at least 10min, changing the water a couple of times if you are using dev. trays.
Tiny white spots/bubbles on the positive
They can mostly be traced back to the dust present on the plate during exposure. Even though we do our best to keep air bubbles to a minimum while coating it is still possible for some micro bubbles to be present on the plate.
SOLUTION: Brush the plate with a flat soft-hair brush before insertion in the dark slide to remove any dust. Bubbles from coating can only be removed with retouching the positive either manually or using adequate software.
HOW TO PRESENT THE POSITIVES?
Well now we come to the most beautiful part of the Dry Plate Tintype process. If you have followed my tips you should be holding a beautiful positive image in your hands.
Silver Gelatine emulsion when dried is pretty rock solid so it really takes quite a bit of effort to put a scratch on it. So if you are doing portraits during a fair or for friends you can simply dry the plates and gift them as they are.
If you wish you can varnish them as well. The mixture that worked well for me was:
70% chroma varnish and 30% turpentine
Pour it on, pour the excess off and let dry on a flat surface.
Or you can simply frame it behind the glass and hang it on a wall for people to admire 🙂
HOW TO STORE THE POSITIVES?
To protect the Dry Plate Tintype Positive from mechanical damage encase it either in a stable plastic sleeve or simply wrap it back in the protective acid free archival paper left over from when you unwrapped fresh Zebra plate. Store them vertically in a tightly packed manuscript box or in a box equipped with grooves.
EXCITING NEWS
We have expanded our product range at Darkroom Chemistry to include Ammonium Thiocyanate in our store. Now, you can conveniently find this essential chemical along with developers, fixers, and other supplies for large format photography. Discover the possibilities and enhance your creative process with ease, all in one place. Get it right HERE.